模具制造時會不可避免的產(chǎn)生一些相關問題,比如說縱裂紋現(xiàn)象的出現(xiàn),對產(chǎn)品還是造成了一定的影響,所以就需要我們先來找找原因然后及時做好處理工作,下面一起來看看問題的相關內(nèi)容吧。
Mold manufacturing will inevitably produce some related problems, such as the occurrence of longitudinal crack phenomenon, or caused a certain impact on the product, so we need to find the reason and then timely processing work, let's take a look at the related content of the problem.
模具拉伸深度過大,鼓脹超過極限,造成縱向裂紋;此外,在精加工時,如果縱向或橫向鼓包超過極限,也會造成破裂。簡而言之,破裂的直接原因是這與鼓脹超限相一致;因此,超過變形極限的開裂在形式上是一種過深的拉深,如果拉深減小,成形條件會變得更好。
The drawing depth of the die is too large, swelling exceeds the limit, resulting in longitudinal cracks; In addition, in finishing, if the longitudinal or lateral bulge exceeds the limit, it will also cause rupture. In short, the immediate cause of the rupture is that it is consistent with a bulge overrun; Therefore, cracking beyond the deformation limit is a kind of too deep drawing in form, if the drawing is reduced, the forming conditions will become better.
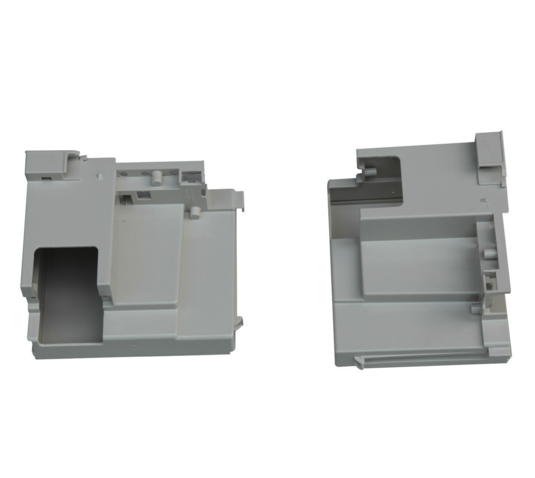
模具的圓角半徑太小,因為是脹形變形,如果超過材料的變形極限,就會產(chǎn)生裂紋;因此,合理的研發(fā)不僅可以防止法蘭產(chǎn)生裂紋,而且可以補充材料。改善材料流入條件的方法之一是增加模具圓角半徑;雖然增加rd可以防止出現(xiàn)裂紋,但此時的半徑比圖紙的尺寸要大。
The fillet radius of the mold is too small, because it is bulging deformation, if the deformation limit of the material is exceeded, it will produce cracks; Therefore, reasonable research and development can not only prevent flange cracks, but also supplement materials. One of the ways to improve the material inflow condition is to increase the radius of mold fillet. Although adding RD can prevent cracks, the radius at this time is larger than the size in the drawing.
山東模具制造廠家認為如果出現(xiàn)裂紋,法蘭部分發(fā)亮,那是因為壓邊力過大。因此,當有破裂的危險時,可以稍微降低壓邊力,觀察產(chǎn)品的變化。模具表面潤滑不足。隨著壓邊力的增加,潤滑油膜的強度也應相應增加,以盡量減少摩擦。如果坯料較大,成型條件會越來越差,因此,有必要將空白減少到一個很小的限度,接近下止點時,坯料應越過拉筋,再進行試拉。
Shandong mold manufacturer thinks that if cracks appear and flange part shines, it is because the blank holder force is too large. Therefore, when there is a risk of rupture, the BHF can be slightly reduced to observe changes in the product. Insufficient lubrication of die surface. As the blank holder force increases, the strength of the lubricating oil film should increase accordingly to minimize friction. If the billet is larger, the forming conditions will become worse and worse, therefore, it is necessary to reduce the blank to a very small limit, close to the bottom dead center, the billet should be over the bar, and then test pull.
How does the longitudinal crack problem occur when the mold is made? The above is the relevant answers to the questions, I hope to give you a good answer, of course, if you need more content to help you understand the mold manufacturing, you can come to our website www.airindiapackersmovers.com for consultation!