一、拋光過度:在日常拋光過程中遇到的問題就是"拋光過度",就是指拋光的時間越長,模具表面的質(zhì)量就越差。發(fā)生拋光過度有二種現(xiàn)象:即是"橘皮"和"點蝕"。拋光過度多發(fā)生于機械拋光。
1、 Excessive polishing: the problem encountered in the daily polishing process is "excessive polishing", which means that the longer the polishing time, the worse the quality of the mold surface. There are two phenomena of excessive polishing: orange peel and pitting. Excessive polishing often occurs in mechanical polishing.
二、工件"橘皮"的措施:當(dāng)發(fā)現(xiàn)表面質(zhì)量拋得不好時,許多人就會增加拋光的壓力和延長拋光的時間,這種作法往往會使表面的質(zhì)量變得差。可采用以下的方法去補救:
2、 Measures to eliminate the "orange peel" of workpieces: when it is found that the surface quality is not polished well, many people will increase the polishing pressure and prolong the polishing time, which often makes the surface quality worse. The following methods can be used to remedy:
(1)把有缺陷的表面去除,研磨的粒度比先前使用砂號略粗一級,然后進行研磨,拋光的力度要比先前的低一些。
(1) Remove the defective surface, grind the particle size slightly thicker than the previous sand number, and then grind it. The polishing force is lower than the previous one.
(2)以低于回火溫度25℃的溫度進行應(yīng)力,在拋光前使用細(xì)的砂號進行研磨,以較輕的力度進行拋光。
(2) Stress relief shall be carried out at a temperature 25 ℃ lower than the tempering temperature. Before polishing, grind with a fine sand number and polish with a light force.
三、工件表面"點蝕"形成的原因
3、 Causes of "pitting corrosion" on workpiece surface
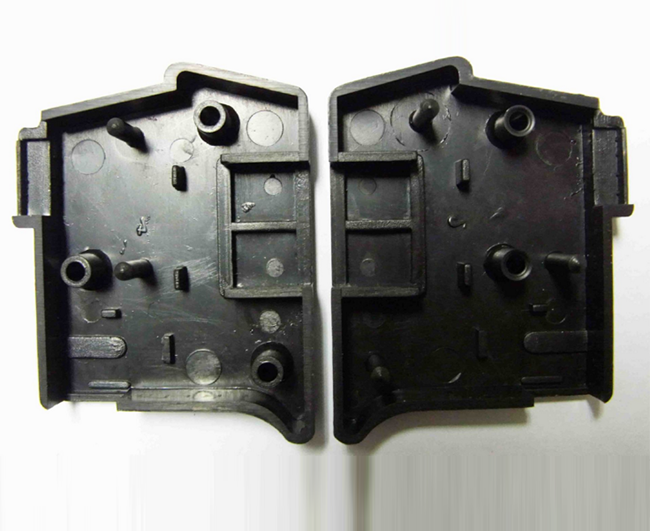
由于在鋼材中有些非金屬的雜質(zhì),通常是硬而脆的氧化物,在拋光過程中從鋼材表面被拉出,形成微坑或點蝕,產(chǎn)生"點蝕"的主要因素有以下幾點:
Some non-metallic impurities in steel, usually hard and brittle oxides, are pulled out from the steel surface during polishing to form micro pits or pitting corrosion. The main factors causing "pitting corrosion" are as follows:
(1)拋光的壓力過大,拋光時間過長。
(1) The polishing pressure is too high and the polishing time is too long.
(2)鋼材的純凈度不夠,硬性雜質(zhì)的含量高。
(2) The purity of steel is not enough and the content of hard impurities is high.
(3)模具表面生銹。
(3) The mold surface is rusty.
(4)黑皮料未。
(4) The black leather is not removed.
(5)小心地將表面重新研磨,砂粒粒度比先前所使用的粒度略粗一級,采用軟質(zhì)及削銳的油石進行后步驟的研磨才再進行拋光程序。
(5) Carefully regrind the surface. The sand particle size is slightly thicker than that previously used. Use soft and sharp oilstone for subsequent grinding before polishing.
(6)當(dāng)砂粒尺寸小于1mm應(yīng)避免采用軟的拋光工具。
(6) When the sand size is less than 1mm, soft polishing tools shall be avoided.
(7)盡可能采用短的拋光時間和小的拋光力度。
(7) Use as short polishing time and small polishing force as possible.
工件出現(xiàn)"橘皮"的原因:不規(guī)則粗糙的表面被稱為"橘皮",產(chǎn)生"橘皮"有許多的原因,常見的原因是由于模具表面過熱或滲碳過度而引起,拋光壓力過大及拋光時間過長是產(chǎn)生"橘皮"的主要原因。比如:拋光輪拋光,拋光輪產(chǎn)生的熱量會很容易造成"橘皮"。較硬的鋼材能承受的拋光壓力會大一些,相對較軟的鋼材容易發(fā)生拋光過度,研究證明產(chǎn)生拋光過度的時間會因鋼材的硬度不同而有所不同。
Reasons for "orange peel" of workpiece: irregular and rough surface is called "orange peel". There are many reasons for "orange peel". The common reasons are caused by overheating or excessive carburization of mold surface. Excessive polishing pressure and too long polishing time are the main reasons for "orange peel". For example: polishing wheel polishing, the heat generated by the polishing wheel will easily cause "orange peel". The harder steel can bear more polishing pressure, and the softer steel is prone to over polishing. The research shows that the time of over polishing varies with the hardness of the steel.